Here Are The Body Parts Scientists Can Print Already
2013.08.17
3D printing finally being put to good use. Here's what scientists can grow, and what you should know.
Team: Cornell University
How it’s made: Scientists take a 3-D scan of a child’s ear, and design a seven part mold in the SolidWorks CAD program. The mold is injected with a high density gel made from 250 million bovine cartilage cells and collagen from rat tails. 15 minutes later, the ear is removed and incubated in cell culture for several days. After three months, the cartilage will have propagated enough to replace the collagen.
Team: Wake Forest Institute For Regenerative Medicine
How It's Made: Deposit multiple types of kidney cells cultivated from cells taken by a biopsy and simultaneously building a scaffold out of biodegradable material. Once transplanted, scaffold will slow biodegrade as functional tissue grows.
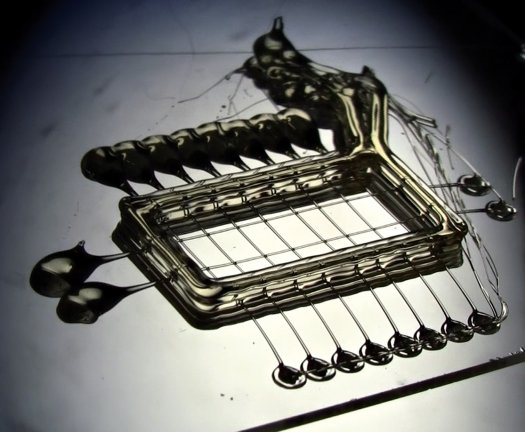
Team: University of Pennsylvania and MIT
How it’s made: The researchers use open source RepRap printer to print a network of sugar filaments inside a mold and coat them in a polymer derived from corn. Then, add gel containing tissue cells into the mold. After that, it is washed, dissolving the sugar and leaving empty channels in the tissue.
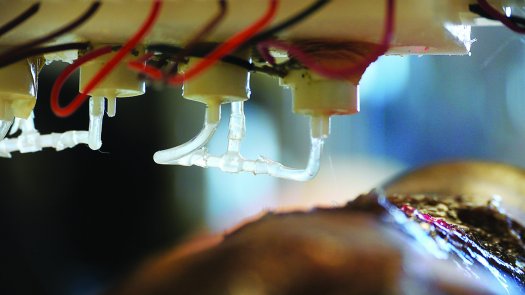
Team: Wake Forest Institute for Regenerative Medicine
How it’s made: Custom bioprinter will scan and map a patient's wound. Inkjet valve ejects the enzyme thrombin and ejects cells mixed with collagen and fibrinogen. It then deposits layer of human fibroblasts, followed by a layer of skin cells.
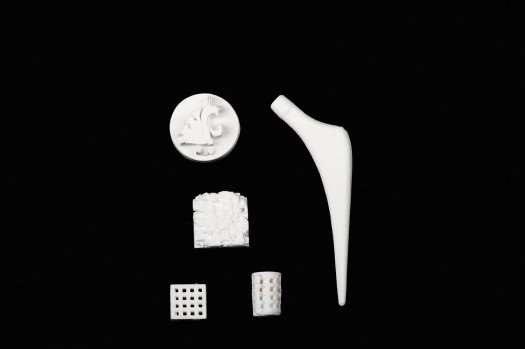
Team: Washington State University
How it’s made: Scaffolds are made with ceramic powder, using the same 3D printers that produce metal parts found in electric motors. Structure is baked at 2,282˚F for 120 minutes and placed into a culture with human bone cells. After a day, the scaffold supports them.
Ears
Ears grown from human cells are more likely to be successfully incorporated into the body.Team: Cornell University
How it’s made: Scientists take a 3-D scan of a child’s ear, and design a seven part mold in the SolidWorks CAD program. The mold is injected with a high density gel made from 250 million bovine cartilage cells and collagen from rat tails. 15 minutes later, the ear is removed and incubated in cell culture for several days. After three months, the cartilage will have propagated enough to replace the collagen.
Kidneys
Team: Wake Forest Institute For Regenerative Medicine
How It's Made: Deposit multiple types of kidney cells cultivated from cells taken by a biopsy and simultaneously building a scaffold out of biodegradable material. Once transplanted, scaffold will slow biodegrade as functional tissue grows.
Blood Vessels
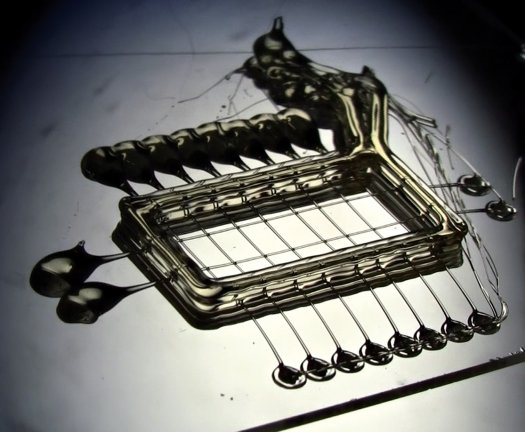
Team: University of Pennsylvania and MIT
How it’s made: The researchers use open source RepRap printer to print a network of sugar filaments inside a mold and coat them in a polymer derived from corn. Then, add gel containing tissue cells into the mold. After that, it is washed, dissolving the sugar and leaving empty channels in the tissue.
Skin Grafts
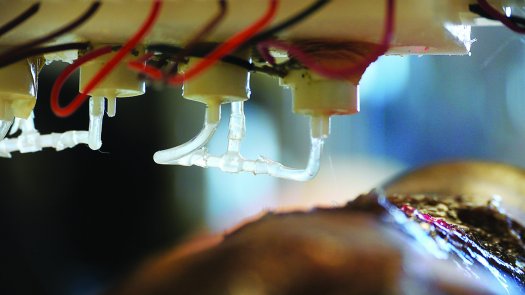
Team: Wake Forest Institute for Regenerative Medicine
How it’s made: Custom bioprinter will scan and map a patient's wound. Inkjet valve ejects the enzyme thrombin and ejects cells mixed with collagen and fibrinogen. It then deposits layer of human fibroblasts, followed by a layer of skin cells.
Bones
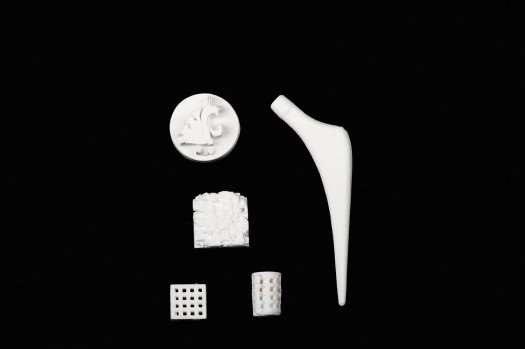
Team: Washington State University
How it’s made: Scaffolds are made with ceramic powder, using the same 3D printers that produce metal parts found in electric motors. Structure is baked at 2,282˚F for 120 minutes and placed into a culture with human bone cells. After a day, the scaffold supports them.
- 3d printing,
- 3d printer,
- medical,
- body parts,
- kidney,
- ears,
- heart,
- skin,
- bones
More Articles
Copyright © Fooyoh.com All rights reserved.